With a length of 6.15 m, the new Vögele Super 1800-5(i) paver is highly compact for its class and ideal for pave widths of between 2.55 and 10 m, anything from city centre measures to paving motorways. Thanks to the new ‘Dash 5’ technology, this Universal Class paver is suited to a wide range of applications, with 129 kW of power and a laydown rate of 700 t/hr.
“The Super 1800-5(i) is two steps ahead of its ‘Dash 3’ predecessors,” said Bastian Fleischer, product manager at Vögele. “We have considerably improved the user-friendliness, sustainability, economic viability and automation in this new generation of pavers.”
The ErgoPlus 5 operating system focuses on the users. Compared to the ‘Dash 3’ version, the paver operator’s console offers improved visibility, better comfort and ergonomics and everything users need for networked road construction. Vögele has simplified the operation of individual functions, enhanced the design, reduced the construction height to increase legroom and integrated additional storage options for mobile phones or similar. Furthermore, the Super 1800-5(i) features more precision steering than its predecessor thanks to Smartwheel. The optional ‘Premium Touch’ display screen allows users to easily monitor and control existing and future digital solutions.
The Paver Access Control (PAC) function and the Light Package Plus also offer greater comfort, efficiency and safety. PAC allows users to operate the Super 1800-5(i) from the ground at the touch of a button. The control unit placed on the screed plate can be used to control all the initial steps safely and conveniently. The optional Light Package Plus provides additional security and reduces set-up times on night construction sites. The LED beamers are integrated into the roof structure and light up the whole operating width of the paver and screed area.
The Super 1800-5(i) has additional assistance and automatic functions to support users. For example, Niveltronic Plus Assist automates the laying of both crown and transverse profiles. Users simply specify the incline of a target point and the machine takes over by gradually approaching this value – which means users no longer need to gradually adjust the incline by hand. The screed width can be automatically controlled along a tensioned wire with the new Edge Control system. The automatic screed width function ensures that the edge and pave width of the screed remain constant when there is no tensioned wire at an exit or entrance.
Reduced fuel consumption and emissions
Even without the new functions, the Super 1800-5(i) features less fuel consumption and lower CO2 and noise emissions. In order to achieve this, Vögele has also reworked the drive concept. The new four-cylinder motor consumes significantly less at the same power. This is primarily due to the optimised Vögele EcoPlus low-emissions package. In particular, the speed-controlled fan has been optimised to calculate the rpm even more accurately and, in conjunction with other measures, substantially minimise noise emissions.
The reworked control of the material transport system also plays an important role in the reduced consumption and increased efficiency. The auger and conveyors now communicate with one another, ensuring that material feed is even more consistent and precisely coordinated. This avoids load peaks, saves fuel, enables an optimum head of mix, therefore allowing uninterrupted paving. In addition, the optional Power Tunnel ensures an optimum material height in front of the screed plate. The retraction and extension of the limiting plates for the auger tunnel can be controlled at the same time as the screed width adjustment.
The Super 1800-5(i) achieves optimum pre-compaction in conjunction with the AB 500 and AB 600 ‘Dash 5’ extending screeds or with SB 300 rigid screed plates. The hydraulic tamper height adjustment ensures excellent paving quality and reduced set-up times. The Dual Power Shift Tamper enables operators to set the tamper stroke easily at the touch of a button. Compared to mechanical adjustment, this saves a lot of time and is very practical, especially with changing layer thicknesses. A new guide and positioning system for fitting screed wideners and more efficient heating of the compacting systems also significantly reduce set-up times. Vögele has further achieved substantial noise level reductions through structural optimisations.
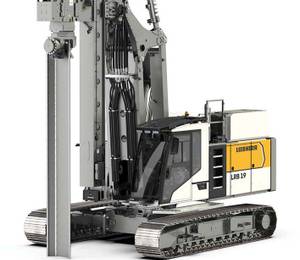
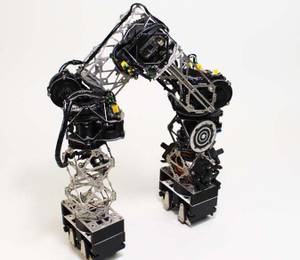
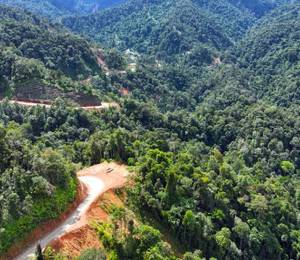
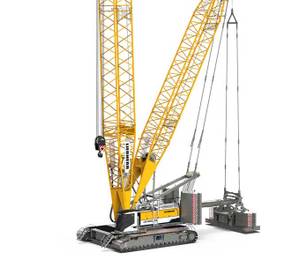
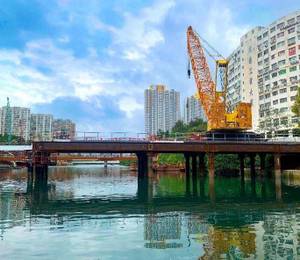
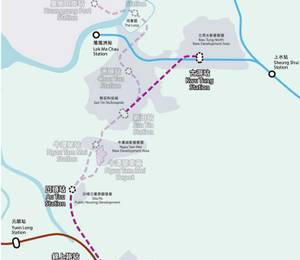
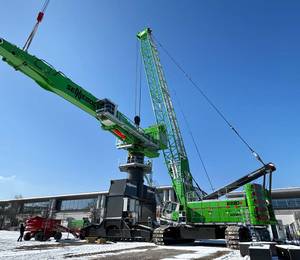