Liebherr’s digital solutions aim to achieve greater efficiency, safe and comfortable operation of machines and systems, as well as time and cost advantages for its customers. During the group’s recent press tour, the global trade media visited the Liebherr-Digital Development Centre in Ulm, Germany, to take a closer look at these technologies.
Central user platforms
MyLiebherr
The central platform for digitalisation is MyLiebherr. All the digital services and offers are bundled together there and made available in an easy-to-understand manner for the respective user. The MyLiebherr portal works across all applications and plays a crucial role in every division of the Liebherr Group.
Tower Crane Portal 2.0
The central digital platform for the tower cranes division has undergone a comprehensive update and is fully integrated into MyLiebherr. The digital crane details have been redesigned and contain all the essential machine data at a glance. Sales information, operating instructions, technical information, data sheets or service forms are all centrally available, including via smartphone.
Planning
MyGuide for Earthmoving
With MyGuide for Earthmoving, Liebherr is launching a new app for earthmoving and material handling machinery specifically for customers and machine operators, as well as fans and anyone else interested in construction machines. This application bundles product information and news from both segments, so that users can access the relevant topics quickly and easily at any time.
Earthmoving Configurator
Inclusion of the Liebherr Earthmoving Configurators directly in the MyGuide for Earthmoving app enables improved operation and application. Users can easily create, save and manage the configuration of their chosen machine at any time via the app. Earthmoving Configurator includes a broad portfolio of machines, attachments, quick coupling systems and services from the areas of earthmoving and material handling machinery. This application is simple and intuitive, and guides the user step by step through the machine design and the available equipment versions and options.
Crane Planner 2.0
With the operation planner for mobile and crawler cranes under MyLiebherr, customers can easily plan crane operations, integrate them into the real environment via Google Maps or generate 3D representations. From this, planning reports (including visibility of all set-up codes, ground pressures, bottlenecks and the required footprints) can be created to show the end customer, without the need for CAD knowledge.
Crane Finder
Upon entering data on the load, required height and desired radius, the Crane Finder displays a range of suitable Liebherr mobile and crawler cranes for the task at hand – including possible configurations. The objective is to find the right crane for a given lifting task quickly and easily. The Crane Finder web application is available free of charge via the MyLiebherr customer portal and can be used on a variety of devices.
Operations and Maintenance
MyLiebherr Maintenance
This digital service enables customers to operate fleets of earthmoving and material handling technology with maximum reliability. Integrated into the MyLiebherr portal, MyLiebherr Maintenance supports plant managers in reducing unscheduled machine downtimes and the time required to identify, assess and resolve issues. For fast troubleshooting, plant managers can view, for example, the machine operator’s MyAssistant damage reports in the service history.
Moreover, MyLiebherr Maintenance can be used to keep an eye on and plan for upcoming maintenance tasks, similar to the machine display. In this way, service activities can be bundled and adapted to operational requirements. Spare parts can easily be ordered in just a few clicks via the MyLiebherr spare parts shop.
MyLiebherr Performance
This digital service is also integrated into the MyLiebherr portal. MyLiebherr Performance enables customers to keep an eye on service data from earthmoving and material handling machines and attachment tools. This helps to identify inefficient machine operations, reduce downtimes, thereby saving fuel, and analyse weighing data. The utilisation overview gives operators a quick overview of how heavily the machines are being used.
An additional feature displays the fuel economy of individual machines and compares them to a global average. With the group comparison function, individual machine groups can be created according to the type of use or the machine category and compared in terms of working hours, downtime and consumption.
Attachment Assist and MiC 4.0 BUS
Liebherr’s Attachment Assist enables smart attachment tool recognition. This solution detects the attachment and transmits its data to the machine. The machine then adjusts automatically to the attachment tool. The data transfer between the machine and the attachment tool is carried out via Bluetooth, so attachment tools can be detected regardless of the quick coupler or manufacturer. All the relevant operational data, like operating hours and coupling times, are recorded and made available online in MyLiebherr Maintenance and MyLiebherr Performance.
Attachment Assist ensures needs-based maintenance, as it reports service intervals and upcoming maintenance. This system uses the new, manufacturer-independent communication standard MiC 4.0 BUS. This makes for significantly easier integration of different attachment tools both with Liebherr machines and with those of other manufacturers.
Digital Mobile Crane Operator
Liebherr offers an eLearning course for digital mobile crane operation, which is carried out online independently and at flexible times. Over 18 units of around 60 minutes each, users are taught the principles of how to handle mobile cranes.
Concrete Connect Portal
The Concrete Connect Portal digitally connects all Liebherr Mischtechnik GmbH machinery related to concrete production, concrete transport and the placement of concrete using concrete pumps. This enables the customer to access individual machine data through to processed information relating to their own Liebherr fleet and thus optimise their working processes. Further functions such as maintenance management and interfaces to other systems within the construction process are in development.
Safety
Safety-relevant assistance systems
To make working with wheel loaders safer, Liebherr has developed an extensive range of assistance systems for the operator. For example, active person recognition automatically differentiates between people and objects using sensors and artificial intelligence. The Skyview 360° camera system uses a number of additional cameras to record the machine surroundings and create a bird’s eye view.
Another example is the weighing device. It is a check weigher that operates automatically and provides the driver with valuable information about the loading process. This is not just used in wheel loaders, but also in the TA 230 Litronic dump truck.
LiReCon (crawler dozer)
The Liebherr Remote Control system is suitable for all crawler dozer applications and increases safety, comfort and productivity, particularly in dangerous working environments. It consists of the Liebherr teleoperation booth, an advanced operator station with all the necessary controls, and the system information: cameras for different viewing angles, microphones for recording machine sounds, and radio transmitters and receivers.
MyNotifier
The monitoring tool for wind conditions and battery status provides the most important data in real time. The wind sensors on the boom of the crawler crane constantly measure the wind speeds. Depending on the length and configuration of the boom, the maximum permitted values are continuously controlled and adjusted.
An early warning system informs the operator in good time of anticipated critical wind speeds. It helps to prevent dangerous situations – for example, the boom can be lowered in advance of critical wind speeds. For the new Liebherr Unplugged machines, MyNotifier has another vital function: The battery status is displayed live.
Performance
Bucket Fill Assist
The new excavator model series from Liebherr is available with the Bucket Fill Assist function. This assistance system has an ‘anti-stalling’ mode, which prevents the bucket from getting stuck in the excavated material. In addition to reducing fuel consumption by 10%, the system minimises any vibrations to make work more comfortable. It also reduces wear on the bucket and in turn lowers the operating costs.
Performance Mobile Cranes
Besides the machine’s location data, the fleet data management solution for mobile and crawler cranes shows a host of other live data, like fuel consumption, current wind speed, the load weight on the hook or when the next service is due for the crane. Customers can also generate their own reports in the system for specifically defined construction sites, e.g. on fuel consumption or CO2 emissions.
From 2023, many new cranes will have the necessary cellular modem on board as standard. Cranes in the field can easily be retrofitted in the future. In any case, Liebherr bears the telecommunications costs.
MyJobsite
This digital tool for deep foundation machines simplifies the documentation of data from a variety of sources and their processing, analysis and translation into relevant information such as performance parameters, construction progress or machine utilisation. Quality control can be performed on that basis for certain tasks on the construction site. This lays the foundations for optimising work processes and ultimately saving time and money.
A list of all the work processes can be stored in MyJobsite. In this way, work steps can be carried out systematically. Machine and process data can be accessed live and is constantly updated. The user always has an overview of scheduled, active and completed jobs and therefore of the current progress of the construction site.
Liduro Power Port app
With the app for the LPO mobile energy storage system, the functions and statuses of a fleet of LPOs can be monitored from anywhere, including the state of charge (SoC), power input and output, energy input and output or geolocation. Fleet managers or rental providers can access advanced functions such as measurement of energy input and output for specific time ranges, definition of loading modes, timer and lock modes and monitoring of all devices and SoCs.
*A quick overview of the 2023 Liebherr global press tour can be seen in this video below. The event was held on 6-7 November 2023 in Ulm and Bad Schussenried, Germany.
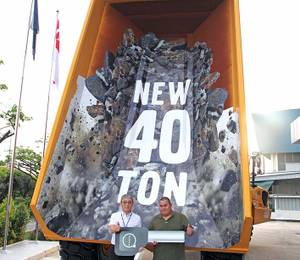
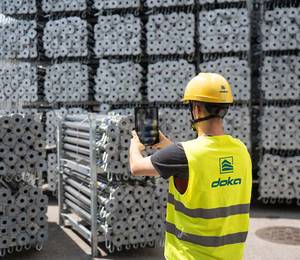
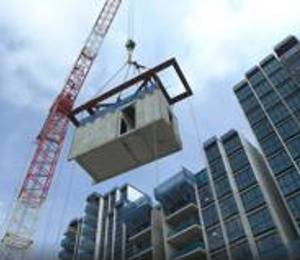
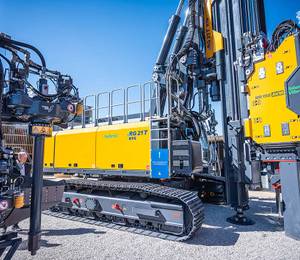
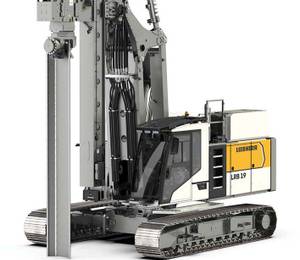
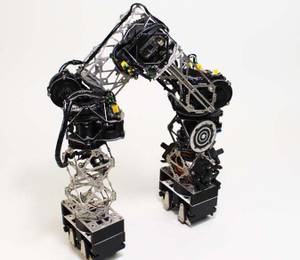
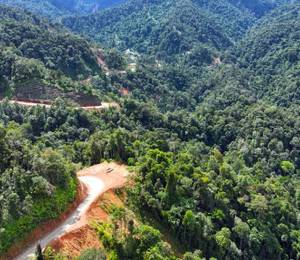