A new private racing circuit has recently been built in Japan, located about 70 km from Tokyo and close to the town of Minamiboso. This 3.5-km circuit features steep downhill gradients of up to 16% and uphill gradients of as much as 19%. The longest straights extend for 800 m and there are also chicanes and tight corners with a 14 m radius.
To deliver this challenging project, paving contractor Maeda Road Construction Co Ltd deployed four Vögele machines, comprising Super 1800-3i and Super 1803-3i Universal Class pavers and a 1900-2 Highway Class paver to complete the paving, while an MT 3000-3i Offset material feeder was used to transfer asphalt from the truck to the material hoppers of the pavers.
The three pavers paved four layers totalling just under 100,000 sq m – an 18-cm non-bonded base course, a 12-cm bonded base course, a 6-cm binder course and a 4-cm surface course. In addition to the racing circuit measuring 36,000 sq m, paving work involved another 60,000 sq m of run-off area, pit lane and service roads. A Super 1900-2 paver was responsible for producing these secondary areas and the base courses.
‘Hot to hot’ paving
The pavers worked mainly ‘hot to hot’: two machines paved together at a slight offset to produce an asphalt surface without joints, measuring 8 to 12 m across the full width of the carriageway. This ensures that the carriageway provides both high resistance to deformation and a long service life.
The different undercarriage concepts also offer a number of benefits. The Super 1800-3i tracked paver is characterised by a high degree of traction and maintains consistent straight-line travel, whilst the Super1803-3i wheeled paver is particularly good at producing corners with a tight radius, as its undercarriage enables the machine to steer sensitively and smoothly. As a result, the paving team used the Super 1803-3i primarily on inside corners.
Meanwhile, the Vögele MT 3000-3i Offset material feeder decouples the transfer of material from the truck to the paver to ensure a constant, efficient paving process. Conical augers in the receiving hopper of the material feeder convey the material crosswise to render it thermally homogeneous.
Furthermore, the material feeder features effective heating of both conveyor and transfer points, actively counteracting cooling and segregation of the material. Another highlight is that, the ‘Offset’ version of the machine has a height-adjustable conveyor that can pivot 55° to the left and right. The discharge point into the extra material hopper of Super pavers can be as high as 3.6 m, optionally up to 3.9 m. It is controlled ergonomically by a joystick.
Despite the extreme grade and slope, the pivoting conveyor meant that on this jobsite, the MT 3000-3i Offset could continuously feed two pavers with material alternately without the need to manoeuvre constantly, thus increasing efficiency and paving quality.
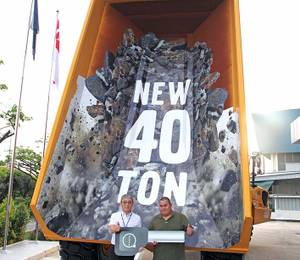
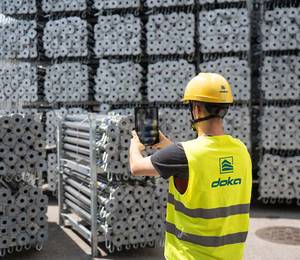
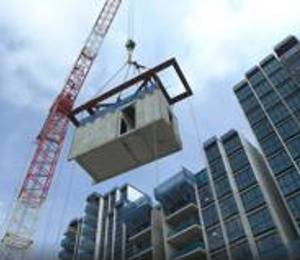
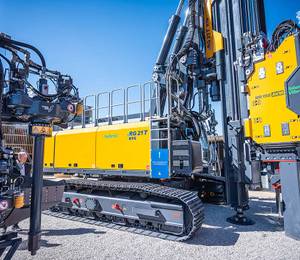
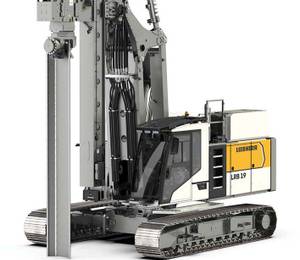
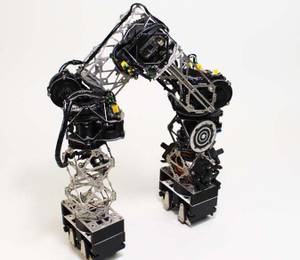
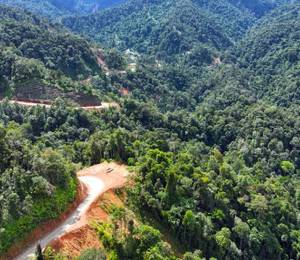