Indonesia’s new national capital Nusantara (‘Ibu Kota Nusantara’ in Indonesian, or IKN) is scheduled to be inaugurated in August 2024, replacing Jakarta. Spanning approximately 2,560 sq km, this newly planned city is located on the east coast of Borneo in East Kalimantan province, surrounded by hilly landscape, forest, and a natural bay.
Being built with a national identity that promotes economic transformation and tourism, the metropolis is utilising artificial intelligence (AI) and advanced technologies to support sustainable transport, renewable energy, and green development. Connecting roads, government offices, utilities, and all necessary infrastructure are being constructed to achieve intelligent, sustainable industrial development, protecting surrounding forests and facilitating zero carbon emissions to become a world-class smart forest city.
As part of this smart city megaproject, 75.62 km of toll road infrastructure is being constructed to improve connectivity and shorten travel times between the city of Balikpapan and the capital’s Central Government Core Area (CGCA) from 2.5 hours to 30 minutes. PT Waskita Karya is the main contractor responsible for the 6.675-km Simpang Tempadung-Jembatan Pulau Balang section 5A of the roadway network, connecting the new IKN VVIP Airport to the CGCA via the existing Pulau Balang Bridge.
“As the main contractor, having a good data communication system between stakeholders is essential to ensure the project is within schedule,” said Indah Nurcahyani, BIM engineer at Waskita Karya.
Various challenges
While the new purpose-built capital is strategically positioned in the middle of the Indonesian archipelago, the area’s topography consists of lush, hilly rainforests dominated by soft soil and clay. “One of the conditions to be considered in determining the design is the extreme terrain, which requires cutting several hills, and the geological conditions, dominated by soft soil and clay layers,” said Ms Nurcahyani.
Compounding these site constraints is the need to align the toll road with the Pulau Balang Bridge, which has already been built. From the initial 3D models, Waskita Karya realised that the basic roadway design plan did not support the existing bridge. “There is a horizontal alignment difference of about 1.5 m; for vertical alignment, there is an average elevation difference of 4 m,” said Ms Nurcahyani.
The difference in distance and elevation between the toll road and bridge had to be discussed with numerous stakeholders located far from the project site, and a design decision reached quickly to keep the project on schedule. To address these design compatibility issues while ensuring structural integrity amid the challenging terrain and tight construction schedule, Waskita Karya wanted to establish a coordinated design review process that allowed for potential design changes, adjusting the toll road to meet the existing bridge parameters.
“The primary and essential focus is reviewing and changing designs quickly, precisely, and accurately,” said Ms Nurcahyani. Waskita Karya needed an easy, fast, and accurate multidiscipline collaboration platform so that the team and stakeholders could virtually visualise and communicate to make timely, optimal decisions regarding design changes.
Collaborative workflows and digital twins
Waskita Karya set up a common data platform using ProjectWise for all participants to access current project information. With iTwin, the team established a real-time, cloud-based design review environment. The team also performed a site survey using drones to capture high-resolution imagery of existing topography and bridge conditions and, using iTwin Capture Modeler (formerly ContextCapture), processed the images into a reality mesh.
“We captured over 10,000 images and processed them in iTwin Capture Modeler, generating a high-fidelity 3D model of the existing bridge that was then uploaded to the cloud,” said Ms Nurcahyani. Integrating Bentley’s open 3D modelling applications, the team created a 3D design model and digital twin of the bridge and toll road.
Working in a collaborative digital environment, Waskita Karya reviewed and commented on the models and performed clash detection to virtually predict potential construction issues. As discussions progressed and the team made decisions regarding design changes, it seamlessly updated and synchronised the models via Bentley’s iTwin Platform, eliminating time-consuming file import and export processes. Field crews also had access to the digital twins via tablets to record their inspections directly on the models.
“Working with the 3D digital twins means that the field team could inspect the basic design plan remotely, record their findings directly on it, and accurately pinpoint the areas in need of repair,” said Ms Nurcahyani. The cloud-based digital twin solution streamlined collaboration among Waskita Karya’s designers and construction personnel, accelerating informed decision-making to ensure bridge and roadway alignment and keep the project moving forward.
‘Saving critical time and costs’
Bentley’s integrated modelling applications provided a connected digital ecosystem to generate digital twins and perform real-time coordinated design reviews, reducing design time by 40% and field inspection time by 50%. “The digital twins provide valuable data and information and function as a communication tool, enabling real-time collaboration and problem solving among the team, without disrupting current processes,” said Ms Nurcahyani. By optimising the horizontal and vertical alignment of the road within a 3D virtual design environment, Waskita Karya saved IDR 12.5 billion in potential rework costs in just the first kilometre of the design plan.
Using Bentley software as an environmental and digital design and construction management platform, Waskita Karya could link multiple data sets, resolving visibility issues and providing accurate material information to construction teams. This practice saved critical time and costs while achieving higher quality deliverables, compared to previous design workflows. The digital twin solution improved communication among engineers, field personnel and stakeholders, eliminating 20,000 truck movements during initial construction and lowering diesel fuel consumption by 32,800 l to save IDR 590 million.
Establishing a connected digital ecosystem and single source of truth enhanced design quality, mitigated risks and provides a solid digital framework for construction. “The project is now under construction, and we anticipate a more accurate design to minimise the need for [on-site] rework and associated costs,” said Ms Nurcahyani.
Image: PT Waskita Karya (Persero) Tbk
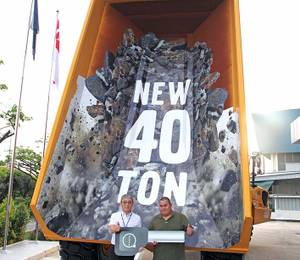
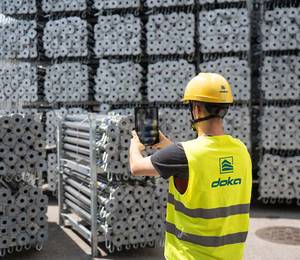
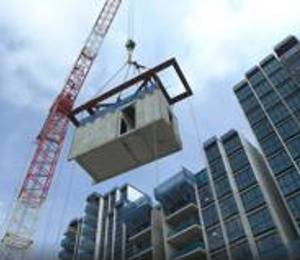
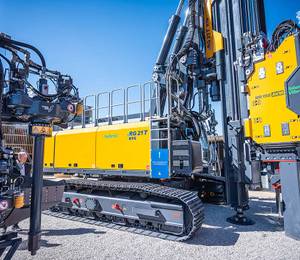
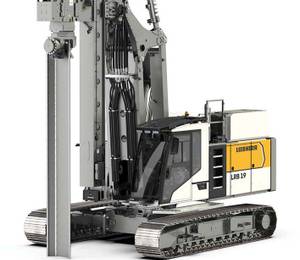
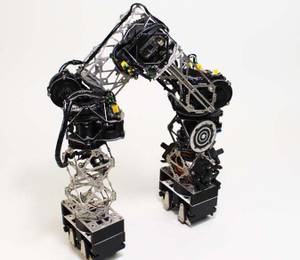
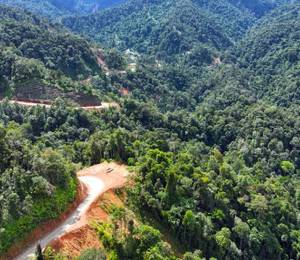