Chinachem Group has announced that its first joint residential development with the Urban Renewal Authority (URA) – Tonkin Street Redevelopment Project – is set to become “Hong Kong’s first private residential project by private developers to adopt concrete modular integrated construction (MiC).”
The project is located at the heart of West Kowloon, covering a site area of about 1,070 sq m. It has a three-sided frontage and will enjoy open views with natural lighting, according to Chinachem. Upon completion, it will provide a maximum total gross floor area (GFA) of about 9,670 sq m.
“The application of MiC will cut down on on-site construction processes and thus the waste generated during construction. We expect a 68% cut on construction waste, a 75% reduction in noise pollution and a reduction in carbon emissions, thereby reducing the nuisance caused to the neighbouring communities,” explained Donald Choi, executive director and CEO of Chinachem Group.
He added that it will also be the first private residential project using MiC that features a terrace, and will make extensive use of “property technology (PropTech)” to improve work quality and efficiency.
Gilbert Tsang, executive director of Gammon Construction, which is part of the project team, said, “Gammon has been joining hands with our partners in promoting sustainable development where MiC plays an integral part. MiC has most processes completed off-site in a factory environment, which is safer and more controlled than the traditional construction site. It enables more efficient quality control for the engineering and commissioning teams, resulting in higher-quality buildings.
“Despite the shortage of construction workers, MiC helps to ensure construction progress as it requires about 70% less on on-site manpower. To facilitate the construction process, Gammon’s digital supply chain monitoring solution, STAMP, will be deployed with data log devices to monitor the delivery and installation of prefabricated components.”
Bryant Lu, vice chairman of Ronald Lu & Partners (RLP), the company responsible for the project design, said, “We are thrilled that Chinachem Group shares our human-centric, sustainability-based design ethos. As one of our fully digitalised projects, using BIM360 and MiC from design through to build created a high level of accuracy and efficiency, saving a full year of design time.
“It is also the first MiC project in Hong Kong’s private sector to be designed with biophilic facade and removable non-structural walls built into the modules, allowing residents to personalise their own living space. The cross ventilation built into each unit brings fresh air into homes and encourage a healthy, low-carbon lifestyle.”
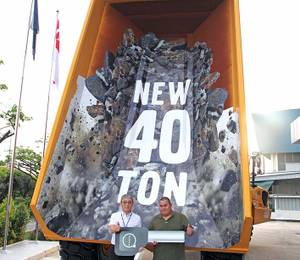
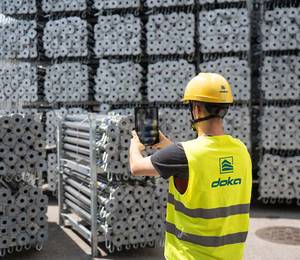
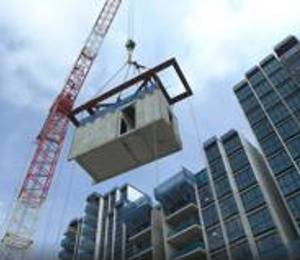
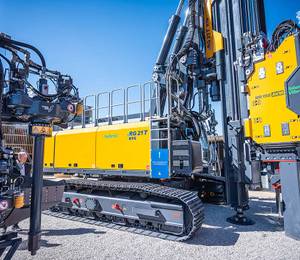
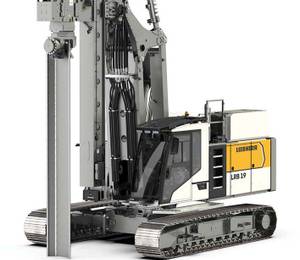
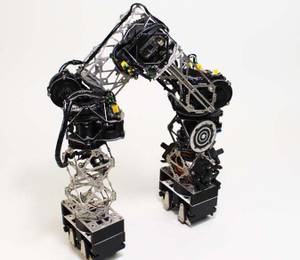
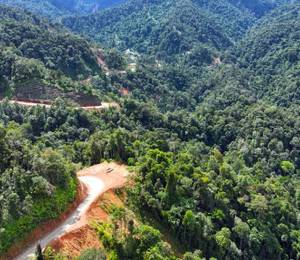