The latest additions to the Cat hammer line-up provide new levels of technology and performance, but are designed with a ‘no frills and no fuss’ approach to deliver great productivity and lower ownership costs for everyday use. They are suitable for use with skid steer loaders, backhoe loaders and excavators in various applications from civil construction, road building, earthmoving, quarrying and mining.
The new, no frills GC-series hammers offer a straightforward design to meet the needs of everyday users by doing away with features that generally add to purchase and operating costs. These economically priced hammers are built with Cat quality – but without the frills. As a result, they are easy to operate, simple to maintain, reliable and durable.
The seven new models added to the Cat range include the H110GC, H115GC, and the new GC silenced-series (H110GCs, H115GCs, H120GCs, H130GCs and H140GCs).
The H110GC and H115 GC are added to the existing GC product line-up comprising the H120 GC (B20), H130 GC (B30) and H140 GC (B35). These two new GC-series hammers are configured for 9.9 – 16.2 t excavators.
The five GC silenced hammers further expand the Cat hammer portfolio by offering additional benefits to customers looking for life cycle value on excavators in the 9.9 – 36.3 t range.
Key features and benefits
The Automatic Shut Off (ASO) feature on H110 GC S – H140 GC silenced (S) hammers offers protection against blank firing, by stopping the piston from cycling internally when there is no material under the tool.
Eliminating blank firing helps protect the hammer from premature damage by reducing internal stresses and heat, and this helps to lower overall hammer ownership and operating costs. Additionally, ASO will protect rental fleet hammers where operator skill level and expertise can vary.
Silencing is standard on the GC S hammers (H110GC S – H140 GC S), which are designed with a protective enclosed housing to minimise overall noise levels on a job site. The standard silencing feature, indicated by the ‘S’ in the nomenclature, protects the operator and everyone near the job site.
Maintenance is also simple on the new range with critical lubrication points made easily accessible, or an optional automatic lubrication system available.
Customers can utilise a carrier mounted auto-lube system or a hammer mounted auto-lube system with the GC silenced hammer range (H110 GC S – H140 GC S). With an optional auto-lube system, the hammer is greased while it runs – saving time and protecting the hammer.
Rental fleets and owner operator customers commonly fit these systems because they could reduce wear and tear and pre-start intervals. Easy and quick access to all other maintenance areas ensures the hammers are ready to operate at their peak and helps to decrease maintenance costs over the life of the tool.
Service of the lower bushing can be carried out in the field using simple hand tools. Users can also verify the gas charge of the hammer without removing it from the carrier. Such a simplified design offers high-level hammer protection as well. The fully enclosed housing protects the power cell, including the front head, cylinder and valve assembly.
A buffer system fitted inside the hammer housing on H110 GC S – H140 GC S models is to protect the carrier from potentially damaging reflective forces. The system also helps to reduce vibration to the machine, improves noise suppression and aids hammer durability. The large top buffer absorbs vibration and prevents damaging impulses from reaching the carrier. The lower and top buffers help to dampen tie rod loading and assist in noise suppression.
An accumulator protects the machine by capturing and buffering hydraulic spikes before they cause damage to hydraulic pumps. Matched with all common carriers, the range is ideally suited to Cat machines as a total solution providing seamless hydraulic connectivity and maximum performance.
Operators can take advantage of simplified design features, such as adjustment of the hammer power via a manual control adjustment on the side of the power cell. The operator can select between high blow frequency and maximum power to get the performance they need to suit their application.
The long stroke - featuring less piston frequency but more impact power and productivity - is best for tougher applications. The short stroke, which has increased piston frequency but with less impact power, is perfect for lighter applications.
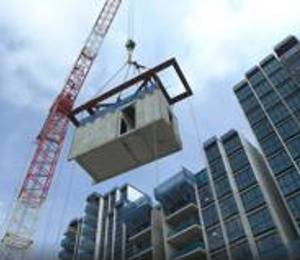
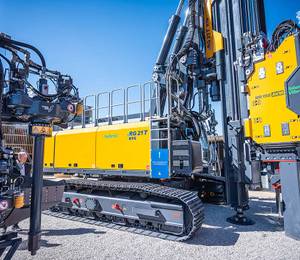
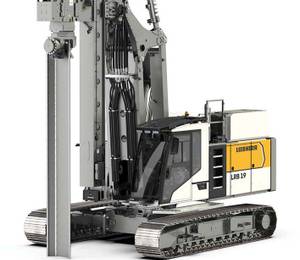
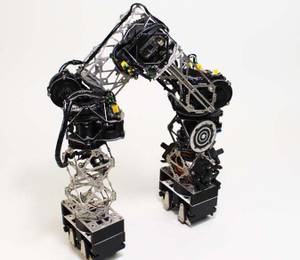
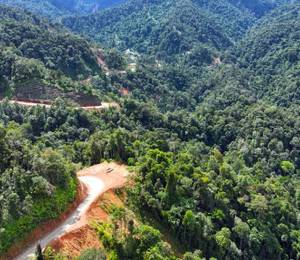
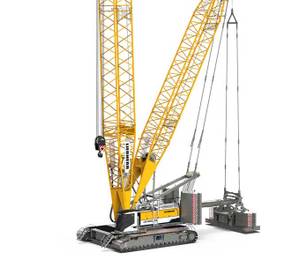
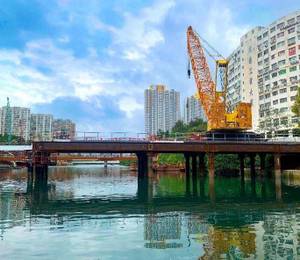